M3 blog
Integrated Maintenance Solutions: Unlocking Operational Efficiency
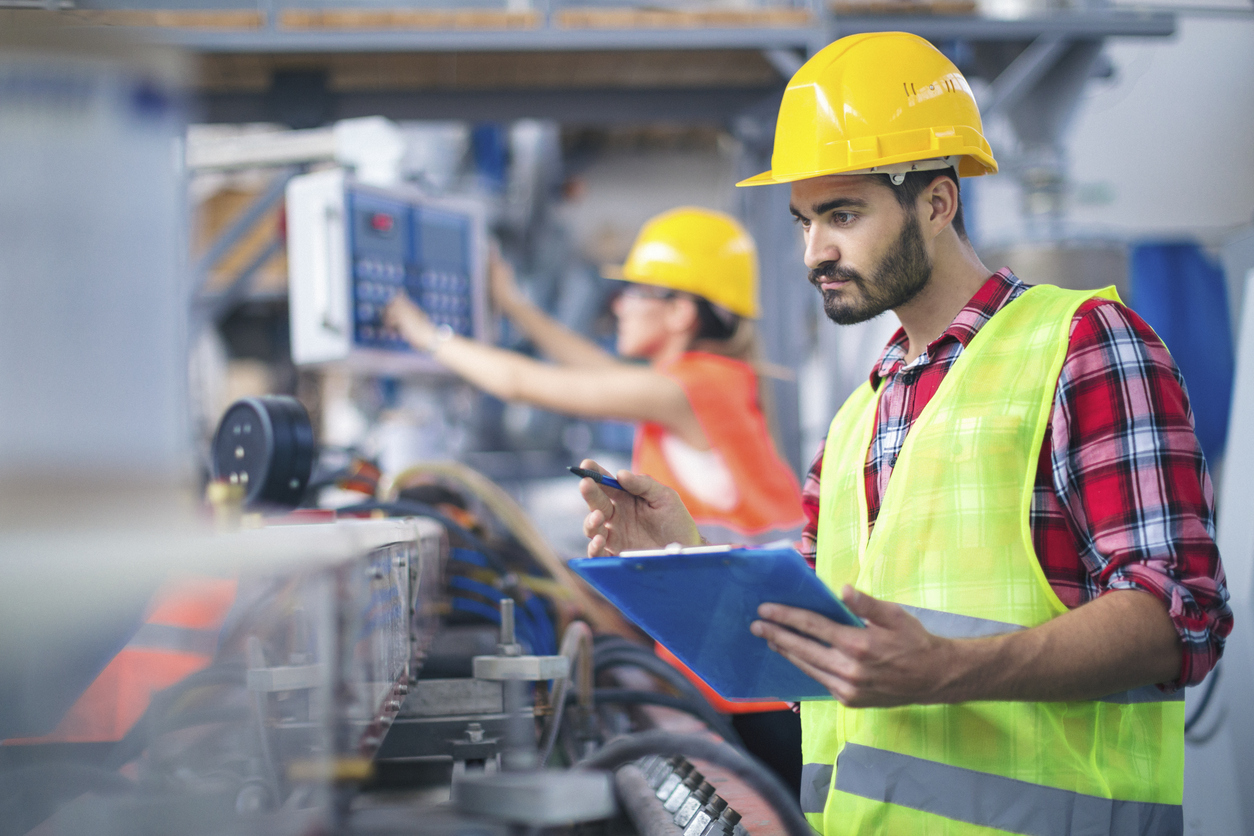
Operational efficiency lies at the heart of any successful maintenance process. Organizations in every industry recognize the critical role that maintenance plays in ensuring seamless operations and delivering quality customer experiences. However, achieving and maintaining operational efficiency within maintenance processes is no easy feat, which is why integrated maintenance solutions have become so critical.
If we take the example of a manufacturing plant where equipment downtime directly translates to production losses or an airline facing costly delays due to unscheduled maintenance. In these scenarios, operational inefficiencies can directly corelate to financial losses, decreased productivity, and even damage to the organization’s reputation.
Operational efficiency in maintenance processes encompasses various aspects, including proactive asset management, timely repairs and inspections, optimized resource allocation, and streamlined workflows. Integrated maintenance solutions offer a holistic approach to address these challenges. By seamlessly integrating various components of the maintenance ecosystem into a unified platform, organizations can maximize operational efficiency.
Concept of Integrated Maintenance Solutions
Traditional maintenance systems often operate in isolation, with separate tools and processes for asset management, work order management, inventory tracking, and data analysis. This siloed approach can result in fragmented data, redundant tasks, and inefficient communication channels, ultimately impeding operational efficiency.
Integrated maintenance solutions offer a holistic approach to maintenance management by seamlessly integrating various components of the maintenance ecosystem into a unified platform. At its core, integrated maintenance solutions aim to break down organizational silos, improve data visibility and accuracy, enhance collaboration among maintenance teams, and streamline workflows from asset tracking to work execution and reporting.
Integrating Device Management Platforms with Existing Maintenance Systems
One of the key components of integrated maintenance solutions is the integration of device management platforms with existing maintenance systems. Device management platforms encompass a range of technologies, including IoT sensors, condition monitoring systems, and asset tracking software, designed to monitor the health and performance of equipment in real-time.
By integrating device management platforms with existing maintenance systems such as CMMS (Computerized Maintenance Management Systems) or EAM (Enterprise Asset Management) software, organizations can achieve seamless data exchange and synchronization. This integration enables maintenance teams to leverage real-time asset data for predictive maintenance, proactive decision-making, and optimized resource allocation.
Integrating device management platforms with existing maintenance systems enhances workflow efficiency by automating data capture, triggering maintenance alerts based on predefined thresholds, and facilitating preventive maintenance scheduling. Ultimately, this integration empowers organizations to unlock new levels of operational efficiency, reduce downtime, and drive continuous improvement in maintenance processes.
Benefits of Integrated Maintenance Systems
- Real-Time Data Accessibility:
Integration allows maintenance teams to access real-time data from device management platforms directly within their existing maintenance systems. This means technicians can instantly view equipment health metrics, diagnostic alerts, and maintenance history without switching between multiple platforms.
This real-time data accessibility empowers maintenance personnel to make informed decisions quickly, prioritize tasks effectively, and respond promptly to equipment issues, minimizing downtime.
- Seamless Data Flow:
Integration facilitates seamless data flow between device management platforms and maintenance systems. Critical asset data, including performance metrics, maintenance schedules, and service history, syncs automatically between the two systems in real-time.
This seamless data flow ensures consistency and accuracy across platforms, eliminating discrepancies and reducing the risk of errors associated with manual data entry or transfer.
- Predictive Maintenance Insights:
Integration enables maintenance systems to leverage predictive maintenance insights generated by device management platforms. By analyzing historical data and equipment trends, predictive algorithms can forecast potential equipment failures or degradation before they occur.
Maintenance teams can proactively address issues, schedule preventive maintenance tasks, and procure necessary parts or resources in advance, optimizing asset uptime and prolonging equipment lifespan.
- Efficient Resource Allocation:
Integrated workflows enable more efficient resource allocation by providing maintenance teams with a comprehensive view of asset health, maintenance schedules, and workload distribution. Managers can assign tasks based on priority, technician availability, and skillset, ensuring optimal resource utilization.
Additionally, integration allows for better coordination between maintenance, procurement, and inventory management functions, ensuring that required parts and resources are available when needed, minimizing delays and downtime.
Seamless Integration with Boeing Toolbox
Boeing Toolbox is a comprehensive suite of digital solutions designed to support aircraft maintenance, operations, and regulatory compliance. It offers a wide range of tools and applications tailored to meet the unique needs of aviation maintenance professionals, including maintenance planning, technical documentation, regulatory compliance management, and fleet management.
Integrated maintenance solutions offer the capability to seamlessly integrate with Boeing Toolbox, providing aviation maintenance operations with enhanced functionality and efficiency. Through API integration and data synchronization capabilities, maintenance systems can exchange information seamlessly with Boeing Toolbox, ensuring that maintenance data, work orders, and compliance records are consistently updated and aligned across platforms.
Boeing Toolbox enables maintenance systems to leverage its rich repository of technical documentation, maintenance manuals, and regulatory information directly within their workflows. Maintenance personnel can access up-to-date information on aircraft systems, components, and maintenance procedures without the need to switch between multiple applications or platforms, streamlining their tasks and improving productivity.
In conclusion, integrated maintenance solutions represent a game-changer in maximizing operational efficiency within maintenance processes. By seamlessly merging various components of the maintenance ecosystem, these solutions optimize resource allocation, streamline workflows, and foster collaboration among teams. Real-time data accessibility empowers proactive decision-making, while predictive maintenance insights preemptively address potential failures, minimizing downtime. Ultimately, integrated maintenance solutions not only mitigate operational inefficiencies but also drive continuous improvement, ensuring sustained business growth.