M3 blog
Safety First: Ensuring Compliance in Aircraft Maintenance
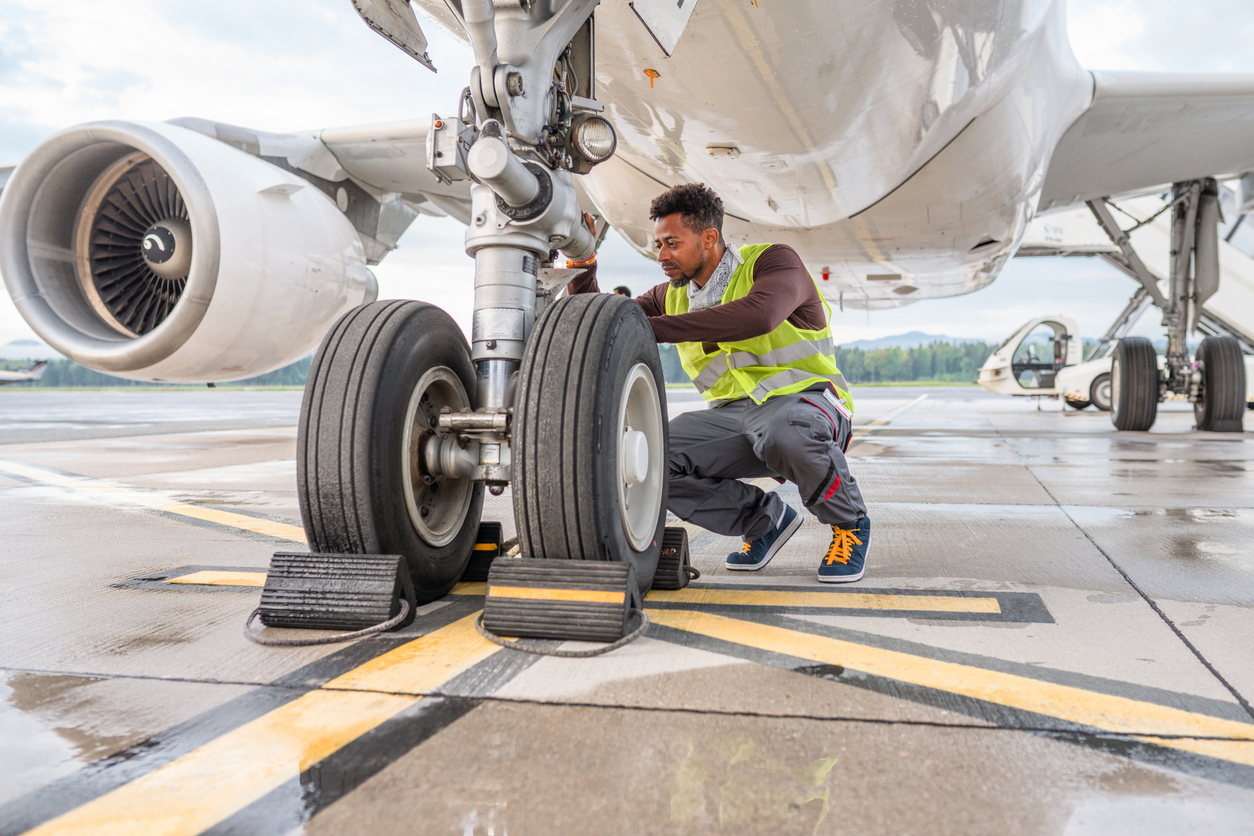
In the high-stakes world of aviation, safety is paramount. The International Air Transport Association (IATA) reports that the global accident rate for commercial flights has been at a historic low in recent years, thanks largely to rigorous maintenance practices and strict regulatory compliance.
In this digital age, Mobile Device Management (MDM) has emerged as a powerful tool for ensuring compliance with FAA (Federal Aviation Administration) and EASA (European Union Aviation Safety Agency) regulations. This blog post will explore how MDM enhances aircraft maintenance safety, operational efficiency, and regulatory adherence.
FAA and EASA Regulations
The FAA, established in 1958, is the national aviation authority of the United States, responsible for regulating all aspects of American civil aviation. Similarly, EASA, formed in 2003, oversees civil aviation safety across European Union member states. Both agencies set stringent standards to ensure the highest levels of safety and operational performance. Both agencies list maintenance as one the key criteria for safety regulations. FAA regulations include FAR (Federal Aviation Regulations) Part 43, which outlines maintenance, preventive maintenance, and alterations, and Part 145, which governs repair stations. EASA’s Part 145 covers similar ground, detailing requirements for the approval of maintenance organizations, while Part M addresses continuing airworthiness. Both agencies demand rigorous documentation, regular inspections, and adherence to approved procedures and standards, ensuring that aircraft maintenance practices consistently meet safety requirements.
The Importance of Compliance
Safety
Compliance with FAA and EASA regulations is fundamental to maintaining aircraft safety. Adherence ensures that all maintenance procedures are performed correctly and that potential issues are identified and addressed before they become serious problems. Regular inspections and preventive maintenance can catch wear and tear early, preventing potential in-flight failures.
Legal and Financial Implications
Non-compliance can lead to significant penalties, including fines and suspension of operating licenses. Airlines found violating maintenance regulations can face hefty fines and even grounding of their fleets. Additionally, non-compliance may affect insurance coverage, increasing liability in the event of an incident. Insurers may refuse to cover damages or hike premiums, leading to substantial financial burdens for the non-compliant entities.
Reputation and Trust
Maintaining regulatory compliance builds trust with passengers, partners, and regulatory bodies. Companies known for rigorous adherence to safety standards enjoy a stronger reputation and customer loyalty. Conversely, lapses in compliance can damage an organization’s reputation, as seen in high-profile cases where non-compliance led to accidents and loss of trust. Incidents involving mechanical failures often result in intense public scrutiny, which can tarnish a company’s image for years.
Key Areas of Compliance in Aircraft Maintenance
Maintenance Procedures
Proper documentation and record-keeping are crucial. This includes detailed logs of inspections, repairs, and maintenance activities. Regular inspections and checks, mandated by FAA and EASA, ensure ongoing airworthiness. FAA regulations require that each part of an aircraft be maintained in accordance with specific guidelines to ensure it remains airworthy.
Training and Certification
Maintenance personnel must be adequately trained and certified. Continuous education and re-certification are essential to keep up with evolving standards and technologies. FAA and EASA both mandate that technicians undergo periodic training to stay current with the latest procedures and technological advancements. This ensures that they can competently perform maintenance tasks and handle any emerging issues.
Use of Approved Parts and Materials
Using parts that meet regulatory standards is critical. Maintenance organizations must verify that all parts and materials used are approved and properly documented. Both FAA and EASA have strict regulations about the sourcing and use of parts, ensuring that only certified components are used in maintenance and repairs. This prevents the use of counterfeit or substandard parts that could compromise aircraft safety.
Quality Assurance and Audits
Regular internal audits and quality checks help ensure compliance. Third-party audits provide an additional layer of assurance, verifying that maintenance practices meet regulatory standards. These audits help identify potential areas of non-compliance and facilitate continuous improvement. An external audit might reveal lapses in documentation or deviations from standard procedures, prompting corrective actions.
Leveraging Mobile Device Management for Compliance
Implementing Mobile Device Management
Mobile Device Management (MDM) systems allow organizations to manage, monitor, and secure mobile devices used by maintenance personnel. By centralizing control over devices, MDM ensures that all mobile activities comply with FAA and EASA regulations. For example, maintenance logs can be updated in real-time, ensuring accuracy and availability for audits.
Real-Time Data Access and Reporting
MDM enables maintenance teams to access and update maintenance records, checklists, and manuals in real-time. This ensures that all documentation is current and compliant with regulatory standards. Real-time data access reduces the risk of errors and ensures that maintenance activities are accurately recorded.
Enhanced Communication and Collaboration
MDM enhances communication and collaboration among maintenance teams. Technicians can instantly share updates, report issues, and access troubleshooting guides, ensuring that maintenance activities are performed efficiently and correctly. This streamlined communication helps in addressing maintenance issues promptly and accurately.
Security and Compliance Monitoring
MDM systems provide robust security features, such as encryption, secure access controls, and remote wipe capabilities, ensuring that sensitive maintenance data is protected. Compliance monitoring tools within MDM can track device usage and ensure that all activities adhere to regulatory requirements. This prevents unauthorized access to critical data and ensures that all maintenance activities are documented and compliant.
Best Practices for Ensuring Compliance with MDM
Developing a Comprehensive MDM Strategy
A comprehensive MDM strategy involves defining clear policies and procedures for device usage, security, and compliance. Organizations should involve key stakeholders, including IT, maintenance, and compliance teams, to develop a strategy that addresses all aspects of mobile device management.
Training and Support
Proper training is essential to ensure that maintenance personnel can effectively use MDM tools. Organizations should provide regular training sessions and support resources to help technicians stay updated with the latest MDM features and compliance requirements.
Continuous Monitoring and Improvement
MDM systems should be continuously monitored to ensure that they are functioning correctly and that all devices remain compliant with FAA and EASA regulations. Regular audits and reviews can help identify potential issues and areas for improvement. Organizations should also stay updated with regulatory changes and adjust their MDM strategies accordingly.
In summary, Mobile Device Management is a powerful tool for ensuring compliance with FAA and EASA regulations in aircraft maintenance. By leveraging MDM, organizations can enhance safety, operational efficiency, and regulatory adherence. Implementing a comprehensive MDM strategy, providing proper training, and continuously monitoring compliance can help maintenance teams stay ahead of regulatory requirements and maintain the highest safety standards.